Understanding the Key Elements of Welding and Quality Testing
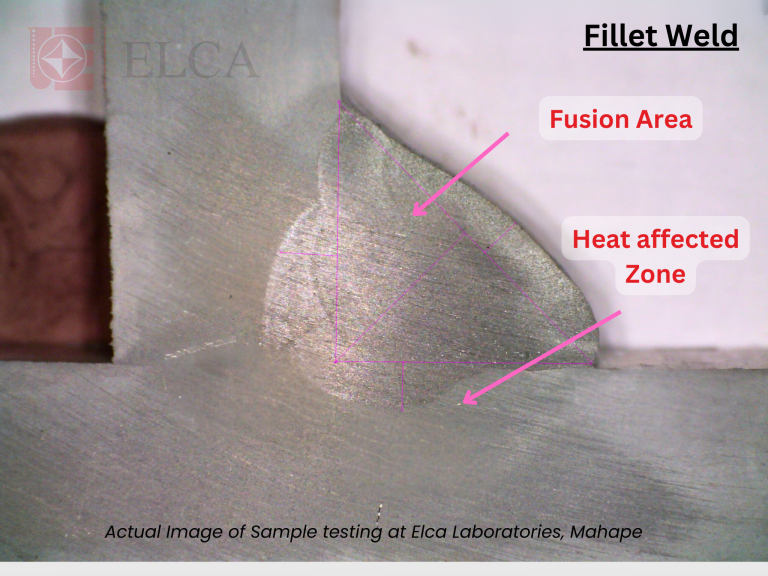
Welding is a fundamental process used across industries to join materials and create strong, lasting structures. Whether it’s in construction, manufacturing, or repairs, ensuring the quality of a weld is critical to its performance and safety. In this post, we explore the essential aspects of welding, the parameters inspected during quality testing, and why maintaining standards is so important.
What is Welding?
Welding is the process of joining two or more pieces of material by melting a portion of each and allowing the liquefied portions to solidify together. This can be done with or without filler metal, and multiple passes may be used to achieve the desired strength.
Critical Areas in a Weld
A weld can be divided into three key regions:
- Fusion Zone – The area where materials have melted and fused together.
- Heat-Affected Zone (HAZ) – The area next to the fusion zone where the material’s properties may have changed due to heat exposure.
- Base Metal – The original material that remains unaffected by the welding process.
Refer to the schematic diagram provided for a detailed visualization.
Sample Preparation for Weld Testing
Testing welds involves preparing samples carefully to reveal their structural integrity and quality. The steps include:
- Cutting a transverse section of the weld joint using abrasive tools.
- Polishing the sample with progressively finer grit papers, followed by final polishing with a diamond cloth.
- Cleaning the sample with water and soap, drying it with hot air, and etching it with a suitable etchant based on the material grade and filler metal.
- Examining the prepared sample under a stereo microscope at 5x to 50x magnification.
Parameters Inspected During Testing
The following defects and characteristics are checked as per IS, ASME, AWS, and EN standards:
- Cracks and laminar tears
- Lack of root fusion, side fusion, and internal fusion
- Lack of root penetration
- Cavities, porosity, and slag inclusions
- Shrinkage, undercut, and excess penetration
- Weld reinforcement shape, leg lengths, throat thickness, convexity, concavity, and penetration depth
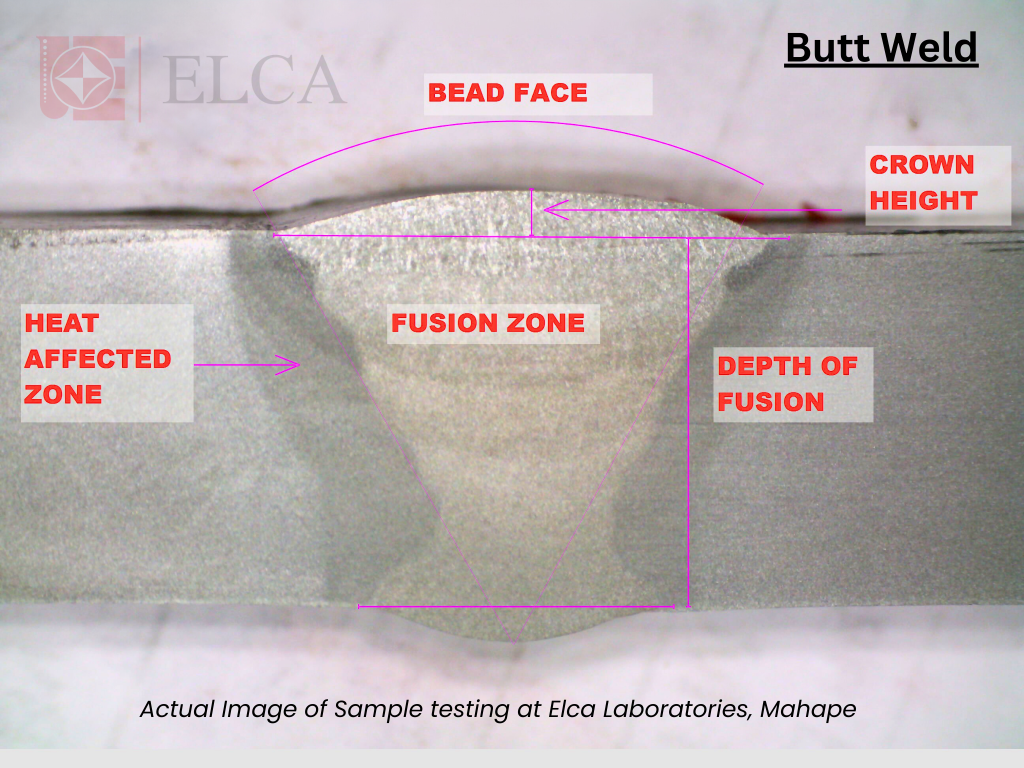
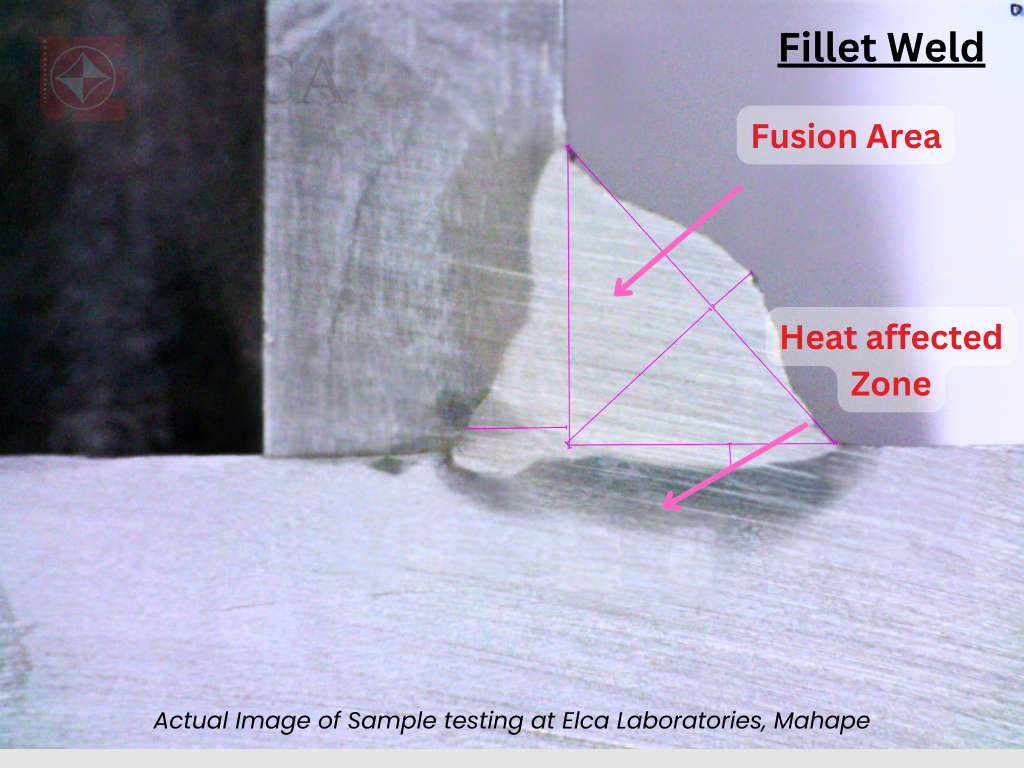
These parameters are critical to ensuring the weld meets both safety and quality standards.